Diving Deep into Die Casting Defects
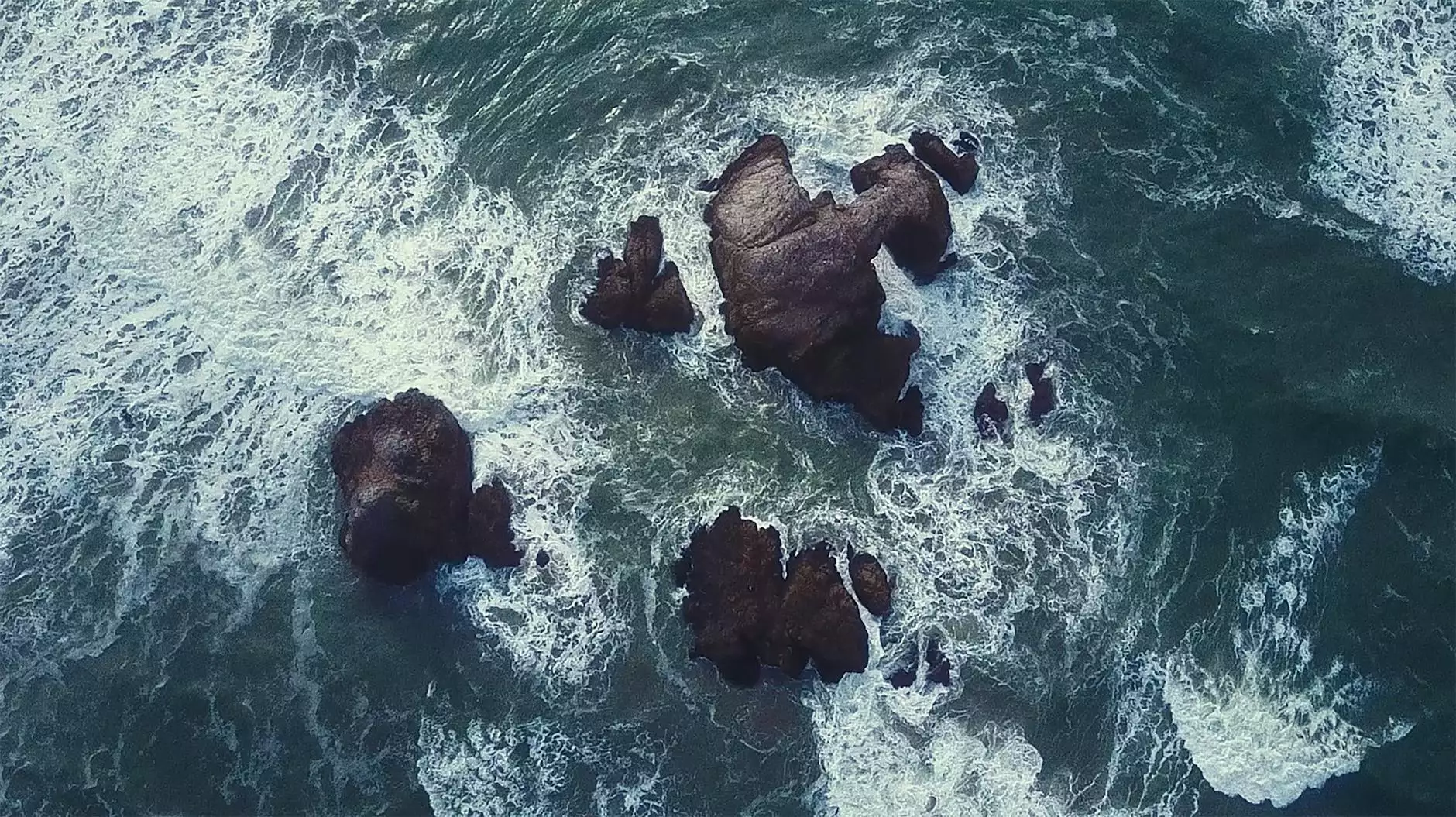
When it comes to producing high-quality die cast products, understanding and minimizing defects is of paramount importance. Wetron Industrial, a renowned player in the Home & Garden Appliances industry, is here to guide you through the intricacies of avoiding die casting defects. In this comprehensive article, we will explore various types of defects, analyze their causes, and provide effective solutions.
1. Understanding the Basics of Die Casting
Before we delve into the topic of die casting defects, it's essential to grasp the fundamentals of the die casting process. Die casting is a manufacturing method that involves injecting molten metal into a mold, which is usually steel. This molten metal is then cooled and solidifies, taking the shape of the mold. The result is a precise and intricately detailed product, commonly used in the production of Home & Garden Appliances.
2. Common Die Casting Defects
Despite the efficiency and precision of die casting, defects can occur. Familiarizing yourself with these defects is the first step towards preventing them. Let's explore some of the most common die casting defects:
2.1 Porosity
Porosity refers to the presence of small voids or air pockets within the die cast product. These voids can significantly reduce the structural integrity of the part and compromise its overall quality. Porosity is often caused by trapped air during the filling stage of the die casting process or due to improper venting.
2.2 Cold Shut
Cold shut occurs when two flowing streams of molten metal fail to properly fuse together, resulting in a visible line or seam on the surface of the die cast part. This defect is commonly caused by inadequate metal flow or insufficient injection pressure.
2.3 Shrinkage
Shrinkage defects manifest as small depressions or voids on the surface of the die cast product. These defects occur due to the contraction of the metal as it cools and solidifies inside the mold. Improper cooling rates or high levels of alloying elements can contribute to shrinkage defects.
2.4 Flash
Flash refers to excess material that escapes between the two halves of the die mold, resulting in thin fins or burrs on the finished product. Flash defects commonly occur due to worn-out or improperly aligned mold components.
2.5 Flow Lines
Flow lines are visible patterns or lines on the surface of the die cast part caused by the movement of molten metal during injection. They can result in a non-uniform appearance and compromised structural integrity. Factors such as high injection speed or complex part geometry can contribute to flow line defects.
3. Solutions to Avoid Die Casting Defects
Now that we have identified the most common die casting defects, let's explore effective solutions to minimize or eliminate them:
3.1 Optimize the Filling Process
To minimize porosity defects, it is crucial to optimize the filling process. This can be achieved by properly venting the mold to allow trapped air to escape, maintaining consistent injection pressure, and utilizing ensuring an even and controlled metal flow.
3.2 Enhance Cooling and Solidification
To prevent shrinkage defects, optimizing the cooling and solidification process is key. It involves analyzing the cooling rates, modifying the mold design to facilitate efficient heat removal, and adjusting alloy compositions to reduce contraction.
3.3 Regular Maintenance of Molds
Preventing flash defects requires regular maintenance of molds. Ensuring proper alignment, eliminating any excessive wear, and addressing any parting line mismatches are crucial steps to eliminate flash defects and achieve a smooth finished product surface.
3.4 Balancing Injection Speed and Pressure
To mitigate flow line defects, finding the balance between injection speed and pressure is crucial. Adjusting these parameters to match the part's geometry and material properties can help achieve a uniform appearance and eliminate flow line defects.
4. The Importance of Quality Control
While implementing the aforementioned solutions is essential, maintaining strict quality control throughout the die casting process is equally important. Wetron Industrial follows rigorous quality assurance protocols to ensure that all finished products meet the highest industry standards. From material inspection to precise dimensional measurements, each step is meticulously tracked and documented to guarantee the consistent delivery of superior die cast products.
5. Conclusion
By understanding the various types of die casting defects and the solutions to prevent them, you are now equipped with valuable knowledge to ensure the production of high-quality die cast products. Wetron Industrial, with its expertise in the Home & Garden Appliances industry, offers unparalleled guidance and services, ensuring the manufacturing of flawless die cast components. By implementing our recommended solutions and adhering to meticulous quality control processes, you can confidently produce superior die cast products that surpass industry standards.