Understanding Compression Molding Companies: Innovations in Electronics and Medical Supplies
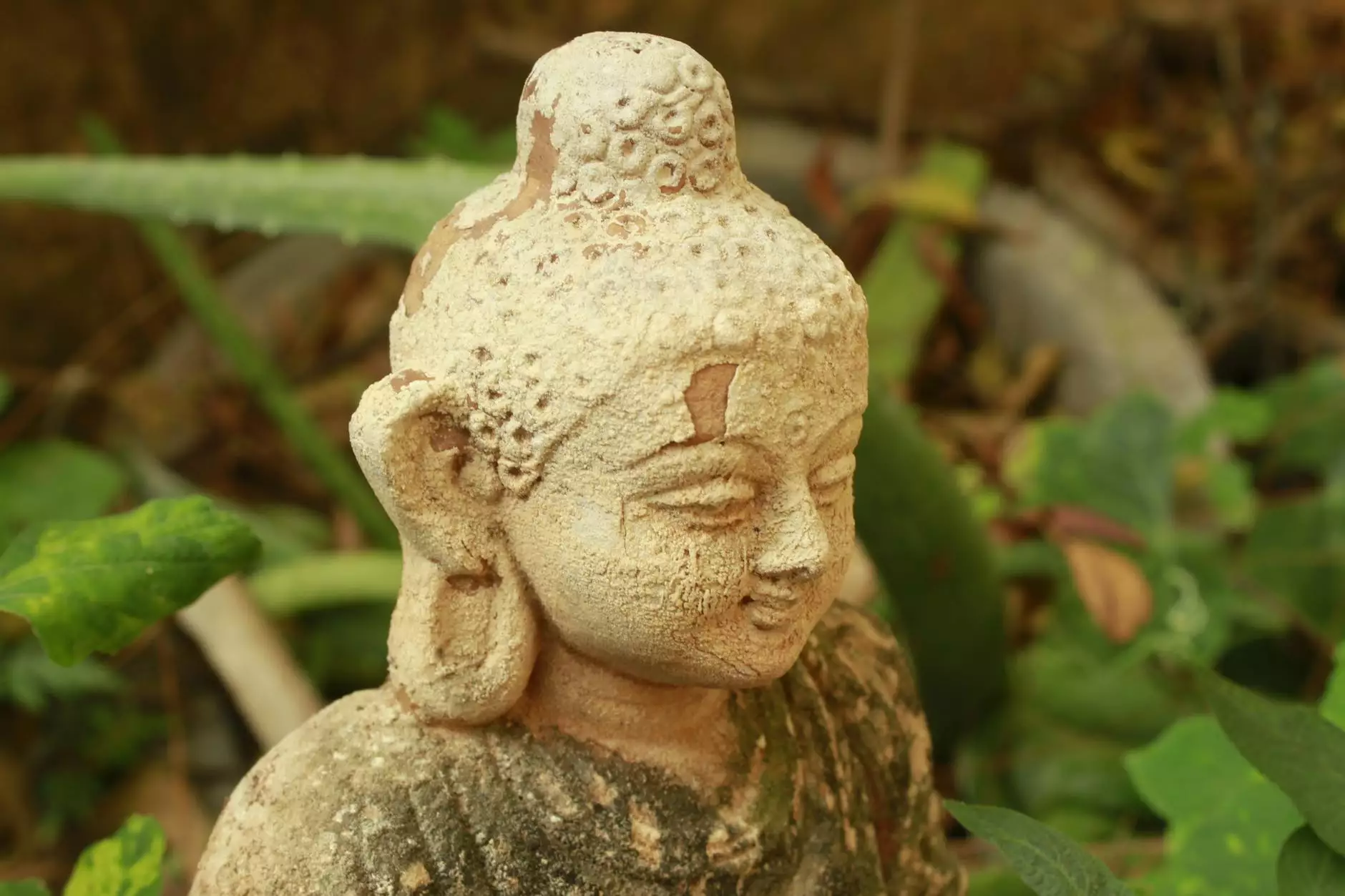
Compression molding is a fascinating and vital manufacturing process that plays a crucial role in various industries, particularly in the realms of electronics and medical supplies. As more businesses seek efficient manufacturing solutions, compression molding companies have become indispensable partners in driving innovation and quality. In this article, we will dive deep into the intricacies of compression molding, its applications in the electronics and medical sectors, and highlight why Nolato.com stands out among other companies in the industry.
The Basics of Compression Molding
Compression molding is a manufacturing process whereby a material is placed in an open, heated mold cavity. The mold is then closed and pressure is applied to shape the material. Some key features of this process include:
- Material Versatility: Various materials, including thermosetting plastics, elastomers, and composites, can be utilized.
- Cost-Effectiveness: This method is particularly advantageous for high-volume production runs, where the cost per unit decreases significantly.
- Minimal Waste: The compression molding process generates less waste compared to other manufacturing techniques, making it an environmentally friendly option.
Why Choose Compression Molding Companies?
Partnering with reputable compression molding companies offers numerous benefits:
- Expertise: These companies bring extensive knowledge and experience in material selection, design, and tooling.
- Quality Control: Leading firms implement rigorous quality control measures to ensure consistent product standards.
- Customization: They provide tailored solutions to meet specific client requirements, ensuring that products are designed to perfection.
Applications in Electronics
In the electronics industry, compression molding is employed to create various components that require durability, precision, and heat resistance. Notable applications include:
1. Housings and Enclosures
Compression molding is commonly used to manufacture housings and enclosures for electronic devices. These parts must be lightweight, yet provide robust protection against environmental factors. The use of thermosetting plastics ensures high-performance levels in terms of heat resistance and electrical insulation.
2. Connectors and Sockets
Connectors and sockets in electronics often require intricate designs to facilitate optimal functionality. Compression molding allows for high-precision parts, ensuring that electronic devices operate efficiently. The process also accommodates complex geometries that enhance interconnectivity.
3. Insulators
Electrical insulation is paramount in electronics. Compression molding companies produce insulators that can withstand high voltages and temperatures, thus ensuring safety and reliability in electronic applications.
Applications in Medical Supplies
The medical sector demands the highest quality standards. Here are crucial applications of compression molding in the medical supplies industry:
1. Surgical Instruments
Many surgical instruments require precision-engineered components that are both sterile and safe for patient use. Compression molding provides manufacturers with the tools to create durable and reliable instruments that meet stringent regulatory standards.
2. Medical Device Housings
Compression molding excels in producing housings for medical devices that need to resist frequent cleaning and sterilization. The materials can be tailored to ensure they are both functional and compliant with health regulations.
3. Drug Delivery Systems
The development of drug delivery systems that incorporate precision dosing mechanisms often relies on compression molded components. These systems must be accurate, reliable, and able to withstand varying environments.
Why Nolato.com Excels in Compression Molding
Nolato.com has established itself as a leader in the field of compression molding companies by adhering to industry best practices. Here are a few reasons why Nolato stands out:
- Innovation: Nolato continuously invests in research and development to adopt new technologies that keep them at the forefront of the industry.
- Quality Assurance: Their robust quality assurance measures ensure that every product meets the highest standards, critical for both electronics and medical applications.
- Customer-Centric Approach: Nolato focuses on understanding their clients’ needs and providing bespoke solutions tailored for their requirements.
The Future of Compression Molding
As industries evolve, the demand for advanced materials and manufacturing techniques will only increase. Compression molding companies will play a critical role in shaping the future of manufacturing through:
- Advanced Materials: The introduction of new thermoplastics and composites will enhance the properties of molded products.
- Automation: Integrating automation into the molding process will increase efficiency and reduce production times.
- Sustainability: Eco-friendly materials and processes will be at the forefront, catering to the growing demand for sustainable manufacturing practices.
Conclusion
In conclusion, the role of compression molding companies is invaluable in sectors like electronics and medical supplies. Their ability to produce high-quality, reliable components while maintaining cost-effectiveness is essential for the progress of these industries. Companies like Nolato.com exemplify excellence in this field, showcasing the importance of innovation and quality in manufacturing. As we look towards the future, the potential of compression molding will continue to expand, driven by technological advances and an unwavering commitment to quality and sustainability.