Understanding the World of China Molds
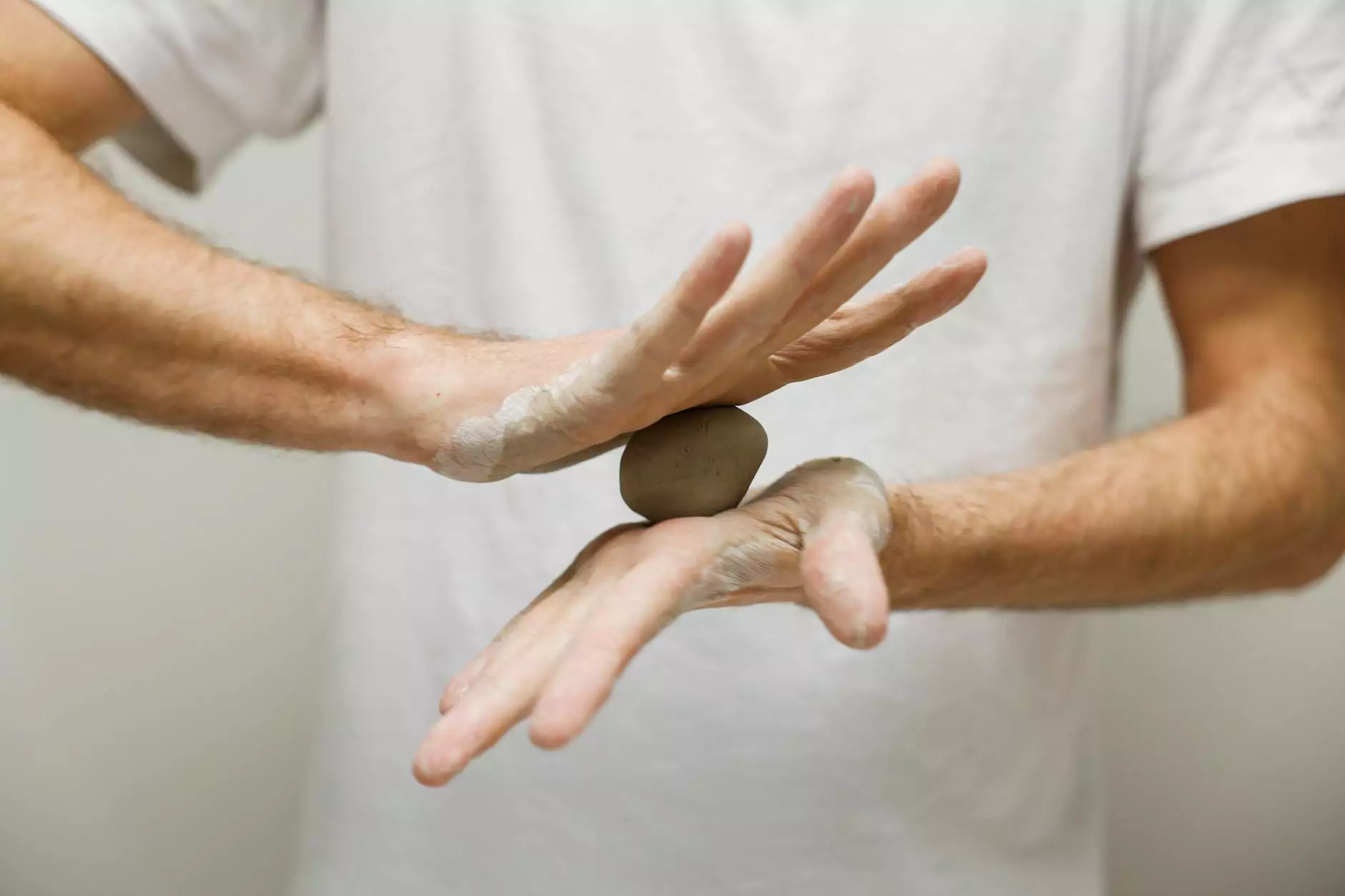
The landscape of manufacturing is changing every day, driven by technological advancements and the rising demand for precision and efficiency. Among the many innovations paving the way for smarter manufacturing processes, China molds have taken center stage, particularly in the realm of plastic injection molding. This article aims to provide an in-depth understanding of what China molds are, their benefits, how they are made, and the significant role they play in the manufacturing industry.
What are China Molds?
China molds refer to various mold types manufactured in China, specifically tailored for plastic injection molding processes. These molds are crucial in the production of plastic parts, allowing manufacturers to produce high-quality components with intricate designs and tight tolerances.
The Importance of Plastic Molding
Plastic molding is central to various industries, including automotive, consumer goods, electronics, and more. The significance can be summarized in the following points:
- High Efficiency: Molding processes enable mass production of plastic parts with minimal waste and maximum accuracy.
- Cost-Effectiveness: Investing in China molds reduces the production costs over time due to high durability and reusability.
- Design Flexibility: Molds allow complex shapes that can satisfy specific functional and aesthetic requirements.
- Consistency: Injection molding ensures that every part produced is uniform, maintaining quality across the board.
Plastic Injection Mould Manufacturing Process
The process of creating China molds can be broken down into several key steps:
1. Design Stage
The first stage involves creating a design blueprint using CAD (Computer-Aided Design) software. This stage is critical, as a well-thought-out design lays the groundwork for the mold's manufacturing process. Key factors to consider include:
- Part Geometry: The shape of the part directly influences the mold design.
- Material Selection: Different plastics require specific mold materials to ensure optimal performance.
- Tolerances: Understanding the required tolerances is vital for functionality.
- Cooling and Ejection Systems: Effective cooling and ejection mechanisms are necessary for efficiency.
2. Mold Making
Once the design is finalized, the actual manufacturing of the mold begins. This involves:
- Machining: Precision machines cut the mold parts from high-grade steel or aluminum.
- Assembly: The individual components are assembled to form the complete mold.
- Surface Treatment: Enhancing the mold surface to reduce wear and improve finish quality.
- Testing: First samples are made and inspected to ensure they meet the required specifications.
3. Injection Molding Process
During the injection molding process, polymer granules are melted and injected into the mold under high pressure. Coolants then solidify the material to create the final part. This stage includes:
- Heating the Plastic: Ensuring that the granules melt completely without degradation.
- Injection: The molten plastic is injected quickly to minimize cycle times.
- Cooling: Crucial for solidifying the part correctly and ensuring dimensional accuracy.
- Ejection: After cooling, parts are ejected, often including repeatable system checks to ensure quality.
Advantages of Using Hanking Mould for China Molds
When it comes to selecting a manufacturer for your plastic molds, Hanking Mould stands out for several essential reasons:
1. Experience and Expertise
With many years of experience in the field, Hanking Mould has honed its skills and knowledge in the production of China molds. This expertise translates into high-quality molds that meet the rigorous demands of modern manufacturing.
2. Advanced Technology
Hanking Mould employs cutting-edge technology and automation in its manufacturing processes. This ensures that all molds produced are precise and capable of high-volume production.
3. Custom Solutions
Understanding that each client has unique needs, Hanking Mould offers customized mold-making solutions designed specifically for your products. Whether you need a simple design or a complex intricate mold, they can accommodate your requests.
4. Quality Control
Hanking Mould has established robust quality control measures at every stage of the manufacturing process. This commitment ensures that the China molds produced consistently meet high standards.
5. Competitive Pricing
While maintaining high quality, Hanking Mould offers competitive pricing structures, making it an attractive option for businesses looking to balance cost with quality.
Applications of China Molds
Plastic molds manufactured in China are used across various industries, showcasing their versatility:
1. Automotive Industry
The automotive sector relies heavily on plastic parts, from dashboards to bumpers. China molds are capable of producing these complex and high-strength components efficiently.
2. Consumer Electronics
With the rapid growth in the electronics market, manufacturers are in constant need of precision plastic parts, including enclosures and connectors, made possible by advanced molding techniques in China.
3. Home Appliances
From refrigerators to washing machines, the safe and reliable plastic components created by China molds make home appliances functional and appealing.
4. Medical Devices
The medical field is increasingly dependent on disposable plastic components which often require highly specific molds, ensuring reliability and safety, available through high-end Chinese manufacturing.
Challenges and Considerations in the Mold-Making Process
While the advantages are substantial, several challenges exist in the mold-making process. Being aware of these can help mitigate potential issues:
1. Initial Costs
The upfront costs associated with mold making can be significant. However, this should be viewed as a long-term investment, since well-crafted molds lead to savings over time.
2. Design Constraints
Designs must account for the capabilities of the molding process, including material restrictions and intricate design limitations that may affect production timelines.
3. Market Volatility
The plastic industry is subject to fluctuations in material costs and availability. Staying informed about market trends is crucial for consistent production.
The Future of China Molds
As technology continues to advance, the future of China molds looks promising. Innovations such as:
- 3D Printing: evolving methodologies are making rapid prototyping and custom mold manufacturing more accessible.
- Sustainable Practices: a push towards eco-friendly materials and processes, aiding the industry as businesses become more environmentally conscious.
- Smart Manufacturing: implementing IoT devices for real-time monitoring of production processes enhances efficiency and reduces downtime.
Conclusion
In summary, the evolution and advancement of China molds and the plastic injection molding industry are crucial for the future of manufacturing. With companies like Hanking Mould leading the charge, businesses can rest assured that they will receive high-quality molds that cater to their specific needs. By integrating advanced technology, diverse applications, and a solid commitment to quality control, Hanking Mould is positioned to continue thriving in the competitive world of plastic mold manufacturing.
Whether you are a small business looking to experiment with innovative designs or a large corporation needing consistent production capabilities, understanding the advantages of China molds will empower you to make informed decisions that drive your business forward.